
- #Cnc Usb Controller Jerky Movements Full Thread Can#
- #Cnc Usb Controller Jerky Movements How To Make One#
Scope of the Research The controller will be built using LabVIEWTM, a graphical programming language produced by National Instruments of Austin, TX, USA.The.
Cnc Usb Controller Jerky Movements Full Thread Can
That control was made way before things were done this way.An issue related to jerky motor movements after clicking the 'stop' button has been reported in the forums. The full thread can be found here The gist of the issue is that: 'I wanted to add to this topic. I’ve been playing with my kit. To develop a driver and an interface circuit between the CNC machine and a PC.
Before any work is done with machine you must be sure that the ‘Gerber’ and ‘NC drill’ files of your PCB design are correct and are generated with correct parameters.The Ethernet SmoothStepper is an external motion control device that connects to. 509Maker s G540 USB CNC Controller is designed to be a plug and play.I would make sure machine parameter 7460 is set to something reasonable (like 10 or 20) just in case that is part of the problem.I assume you are running in FE mode and have tried setting the baud rate up (has to be done at both ends)?Have you tried setting the serial interface to an EXT mode and using something other than TncServer? I think the 355 should go to 38K baud. Here is a link to the Heidenhain data interface manual, in case you don't have it. 9600 baud should get you at least 600-700 characters/sec, if there are 25 characters on a line average then that is 25 or 30 lines a second. If you are doing HSM paths with bunches of little line segments at high feed, lets say 400 ipm then that's 6.6 inches per second or only 4 or 5 lines/inch of machining before you starve.
Indeed, there are many projects out there where someone converted a manual rotab to become a 4th axis. In the second, we’ll look at how they work.If you’re new to CNC, your first impression may be that the 4th axis is used in the same way a rotary table is used for manual machining. In the first installment, we’ll look at what a 4th axis is used for. This is an article series to help beginners understand how and why a 4th Axis is used on CNC Mills. Haas actually got it’s start building a 4th axisbefore it ever built entire CNC machines (pictured on the right).
In fact, there are some types which are called “indexers” that can only be used to index in fixed degree increments rather than continuously rotating to any desired position. When indexing, no cutting happens until the 4th axis is stopped (and often locked with a brake of some kind). A 4th axis is typically either used in an “indexing” mode or a “continuous” mode. But there are also many other applications.First thing to talk about is this term “indexing”. There are cases where we do continuous machining with a 4th axis–in other words, we want the cutter to be machining as the 4th axis turns. With CNC, cutting along an arc is easy–that’s what the G02 and G03 g-codes are for.
It’s very powerful, but plenty of work (perhaps even the majority of 4th axis work) is done simply with indexing.The most obvious case for indexing is to gain better access to the part. Also, you’ll need much fancier CAM software to program continous machining. For example, to produce a cam lobe.You may wonder why you’d ever want anything but continuous machining, but bear with me–there are lots of useful ways to take advantage of indexing.
Cnc Usb Controller Jerky Movements How To Make One
Suppose you have a part like a throttle body that has holes on all sides. But, there are much simpler cases where indexing is also extremely helpful. They the next tooth is indexed into position.Gears are kind of an extreme case because it would be hard to imagine how to make one if we couldn’t index the teeth.
As you can see, they have things set up so they can even do more than one kind of part on a tombstone. They load and unload the tombstone (which is the big upright chunk of cast iron the parts are held to while machining) while the machine is busy cutting new parts on a tombstone in the machine. But another reason is that almost any Horizontal Mill has a 4th Axis Tombstone arrangement:A 4th Axis Tombstone on a Horizontal Mill…Pictured is a great example from our article on a successful manufacturer that is so productive with their Horizontal Mills they only need 2 1/2 machinists–it’s a family business. One reason is that the chips are easier to keep clear on a Horizontal since gravity is helping rather than forcing them further down into the hole where they’re harder to get at. Or, you could also use a 4th axis to index the sides so more than one can be machined with a single setup.In a future article, we’ll get into programming 4th axis indexing.They say that Horizontal Machining Centers can be tremendously more productive than Vertical Machining Centers.
The ballnose has a weakness, which is that the closer you get to the tip, the slower the flutes are spinning. This can be surprisingly effective, but is seldom as powerful as true Continuous Machining.The second advantage comes when profiling with a ballnose cutter. The closest thing possible without continuous machining would be to index as many positions as possible and use 3D contouring toolpaths to try to get the job done. First, you can machine shapes that would otherwise be impossible or very difficult. This video of a turbine blade being machined makes the difference between continuous machining and indexing pretty obvious:There are a couple of advantages to Continuous Machining. 4th Axis Continuous MachiningNow comes the fancy stuff: 4th Axis Continuous Machining, which may also be referred to as “4th Axis Contouring”.
You could lay out a 2 1/2D engraving on a flat surface, and then if you had some way to “wrap” that engraving around the cylinder, it would come out right. Imagine you want to engrave some text on the side of a cylinder. With this technique, you use the 4th axis to allow the ballnose to be presented to the workpiece at an angle, so the side of the ball is used more than the tip:Not only does this allow faster milling (higher feedrates are possible) but it gives a better surface finish and even improves tool life.I’d be remiss if I didn’t mention the special case of 4th Axis Continous Machining which is called wrapping. Conceptually, the exact tip isn’t really moving at all as it is a circle with zero radius.This observation leads to a clever technique called “Sturz Milling”. Hence, the tip moves slower. The ones near the tip are smaller circles, their circumference is shorter, yet they’re spinning at exactly the same rpm as the bigger circles up higher.
How do Tombstones Increase Work Area on a CNC with 4th Axis?A tombstone with fixtures on all four sides set up on a Tormach CNC Mill…I was reading an article about Tombstones in the Tormach blog recently and it got me to thinking about how Tombstones on VMC’s can make a job more profitable.Tombstones are par for the course on Horizontal Machine Centers, but they’re seen a lot less often on Vertical Machining Centers. Depending on the size of the part, you made need an offset arrangement more like the Stallion version pictured above. You’re typically putting parts on or off the fixture plates while the machine is running and as soon as it stops, you swap either the fixture plates or the whole tombstone to get the machine running again quickly. Here’s one I’ve shown before from a big horizontal milling setup:The vertical mill version is similar, but typically a bit smaller:The goals with Tombstones are usually to get access to more parts, more sides, and to make swapping many parts into and out of the machine go fast. There are many different shapes and sizes of Tombstones available for 4th Axes. It enables all new kinds of machining and can also make existing jobs run faster and require less setup.4th Axis Tombstones = Mill Table Fixture PlatesTombstones correspond to Fixture Plates on a mill.
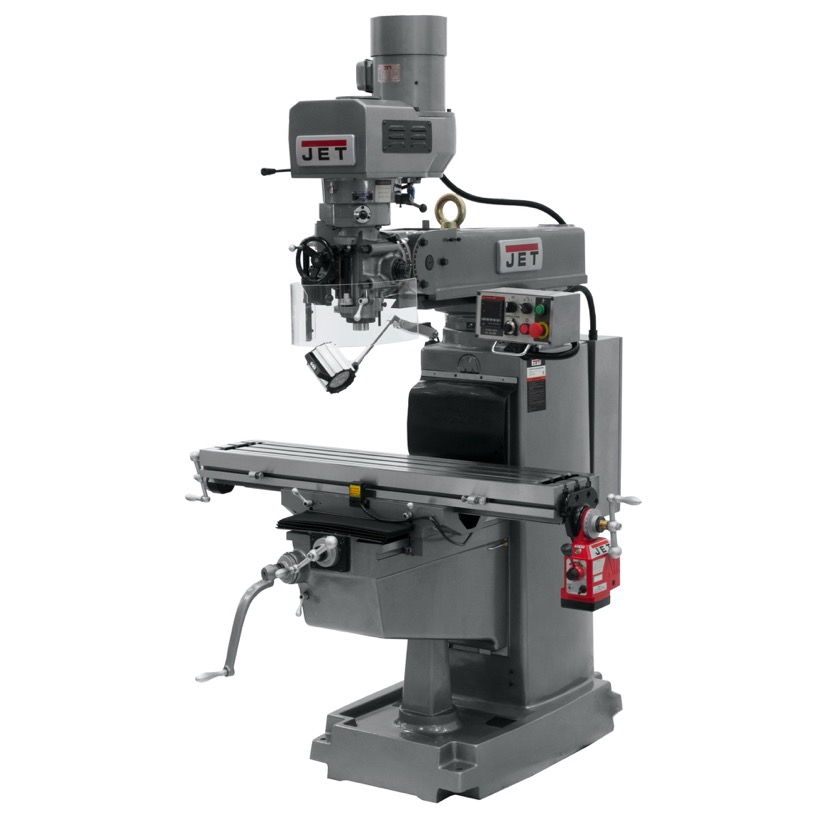
In fact the width of the tombstone is 4″and the length is 13″, so counting all 4 sides, you get 4 x 4 x 13 = 208 square inches. It’s like having 4 smaller tables available. So, that’s 171 square inches you can utilize for making parts–fit as many in as you can!Now consider a tombstone like the one pictured above. The more the merrier because your setup time divided among all the parts will invariably be less on a per part basis.With that in mind, why not think of that Tombstone in the 4th Axis as being all about creating more addressable table surface area?On a Tormach PCNC 1100, you get 18 inches of X and 9.5 inches of Y travel.
That’s not bad!In addition, we can machine 3 faces on each part. So, for about every 4 parts we can fit 1 part gets a free ride.
